VISION WIDE TECH CO., LTD.
- Address: No. 1126-2, Bishan Rd., Caotun Township, Nantou 54258, Taiwan
- Tel: 886-49-2338888
- Fax: 886-49-2330083
- mail: info@visionwide.com.tw
- Privacy Policy
- 2018 Vision Wide Tech All Right Reserved
Heavy Duty Double Column Machining Center
- Home
- Products
- 5-face Double Column Machining Center
- Heavy Duty Double Column Machining Center VB Series
VB Series
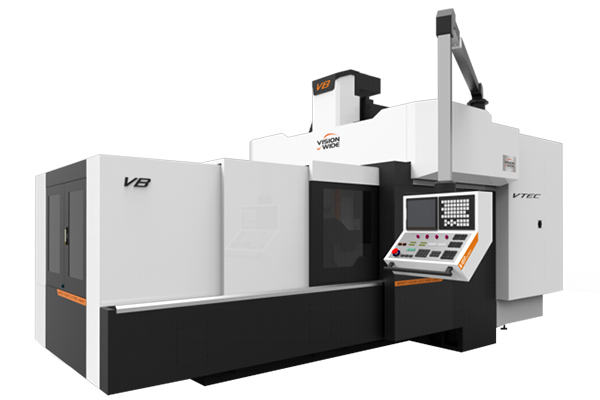
-
VB series, a CNC milling double column/ bridge machining center, applied box guide ways to display Vision Wide’s delicate scrapping and traditional machinery techniques. VB is equipped with extraordinary heavy duty cutting ability that met cutting requirements for mold base and components. Meanwhile, there were auto heads attachments for mold surface machining.
- Three axes movement is fully supported by Harden box way with low friction.
- Box ways were heat treated to HRC 50 hardness, and were precisely hand scrapped, then assemble and tune to the best accuracy to ensure smooth and precise feeding performance.
- Box-shape with ribs design, main casting structure parts are made of Meehanite grade casting iron with stress- relief heat treatment provides durable, rigid support of the machine.
- Large size Guide ways are designed with optimal span to carry the table, box-shape bed with strong V-shape enforced ribs allows heavy workpiece load.
- The best center-line layout of the spindle system, the spindle is close to the Y box way reducing the unbalanced cutting moment and offset thermal expansion to a minimum.
-
Model Unit VB-2016 VB-2516 VB-3016 VB-2020 VB-2520 VB-3020 VB-4020 X axis travel mm 2,000 2,500 3,100 2,000 2,500 3,100 4,100 Y axis travel mm 1,600 2,000 Z axis travel mm 800/1,020(OPT.) 800/1,020(OPT..) Table dimension mm 2,000×1,300 2,500×1,300 3,100×1,300 2,000×1,700 2,500×1,700 3,100×1,700 4,100×1,700 Max. table load kg 8,000 9,000 10,000 9,000 10,000 11,000 12,000 Spindle motor power
(cont./ 30 min rated)kW 18.5/22 (22/26 OPT.)(30/37 OPT.) 18.5/22 (22/26 OPT.)(30/37 OPT.) Spindle speed 2-step gear rpm 4,000/6,000(OPT.) 4,000/6,000(OPT.) Cutting feed rate mm/min 1-7,000 1-7000 Rapid traverse (X/Y/Z) m/min X/Y/Z:15 X Y:12 Z:15 X/Y/Z:15 X/Y:12,Z:15 ATC capacity pcs 32/40(OPT.) 32/40(OPT.) ※Please contact sales for more details.
-
Standard Accessory & Function- Fanuc 0iMF PLUS Controller
- 4,000 rpm two-step gear spindle
- Spindle oil cooler
- Twin hydraulic cylinders with pressured air assistance balancing system
- X-axis ball screw supporter ( X > 4m above)
- Centralized auto lubrication system
- Independent lubrication oil collector
- Ball screw cooling system
- Air blast through spindle
- Wash gun and pneumatic interface
- Cutting fluid cooling system
- 40 tools magazine with arm type ATC
- Enclosed sheet metal guard without roof
- Swiveling arm type operation panel
- Screw type chip conveyor on table sides
- Caterpillar type chip conveyor / Water tank
- Heat exchanger for electrical cabinet
- Working lamp
- Operation cycle finish and alarm light
- Movable manual pulse generator
- Footswitch for tool clamping
- RJ45 interface
- XYZ-axis absolute pulse coder feedback
- XYZ-axis travel hard limits protection
- Spindle cutting load software protection
- Remote monitoring software-Standard (Not available for Siemens controller)
- Auto power off
- Vision Wide FX graphical user interface
- Foundation pads and bolts kits
- Adjustment tool and tool kits
- Technical manuals (operation, maintenance manual and circuit diagram)
Optional Accessory & Function- 6,000 rpm 2-step gear spindle
- Z-axis travel 1,020mm
- 200 / 300 / 400 / 500 mm higher column
- The interface of coolant through spindle
- Coolant through spindle system 20 / 70 bar
- Coolant through tool holder interface
- Coolant through tool holder 5 / 20 bar cutting fluid interface
- Oil skimmer
- Oil mist cooling device (MQL)
- Spindle ring cutting coolant device (for no head attachment)
- 60 tools magazine with arm type ATC
- Enclosed sheet metal guard (with roof)
- Helical blade screw conveyor on table sides
- Chip cart
- Air conditioner for electrical cabinet
- X/Y/Z axis linear scale
- XYZ axis independent manual pulse generator
- Sub table
- Rotary table
- Interface reserved for fourth axis
- Tool axis retract function at power failure
- Anti-collision and machining simulation software
- Remote monitoring software (professional)
- Auto workpiece measurement
- Auto tool length measurement
- Transformer
- Auto warm up
-
VB Series